LKT ist 2020 mehrfacher Innovationspreisträger im Leichtbau
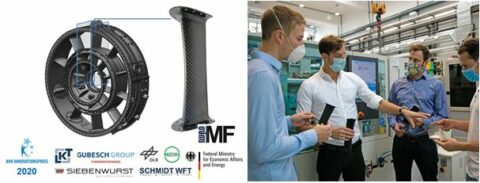
Der Lehrstuhl für Kunststofftechnik hat mit dem Verfahren Duro-IMF zur „Material- und energieeffizienten Herstellung von Turbinen Struts durch die integrative Kombination duroplastischer faserverstärkter Werkstoffe“ den JEC Innovation Award in der Kategorie „Aerospace“ gewonnen. Die Auszeichnung wird jährlich für die innovativsten Projekte im Bereich der Faserverbundtechnologie vergeben und erfolgte, aufgrund von Covid-19, Online im Rahmen der JEC Digital Korea am 25. November 2020.
Neben dem JEC Innovation Award hatte der LKT kurz zuvor am 12. November 2020 ebenfalls mit dem Projekt „Duro-IMF“ den 3. Preis als Gewinner des AVK-Innovationspreises 2020 in der Kategorie „Forschung/Wissenschaft“ erhalten. Die Preisverleihung erfolgte durch die AVKVorstandschaft im Rahmen der Composite for Europe digital. Mit dem AVK-Innovationspreis werden jährlich Universitäten, Hochschulen und Institute für herausragende wissenschaftliche Arbeiten in Forschung und Wissenschaft mit besonderem Augenmerk auf das Thema „Nachhaltigkeit“ ausgezeichnet.
Hintergrund: Das Duro-IMF Verfahren wurde unter den förderpolitischen Zielen „Leistungsfähige und effiziente Luftfahrt“ und „Umweltfreundliche Luftfahrt“ im gleichnamigen Verbundprojekt Duro-IMF (Fkz. 20W1503D) mit den Partnern Deutsches Zentrum für Luft- und Raumfahrt, Siebenwurst, Schmidt WFT, Gubesch Group und Raschig am LKT entwickelt.
Gefördert wurde das Projekt durch das Bundesministerium für Wirtschaft und Energie. Duro- IMF ist eine neue Verfahrenstechnologie zur integrativen Herstellung von duroplastischen Hybridbauteilen wie z. B. eines Turbinen Struts. Das neue Verfahren kombiniert hierfür endlosfaserverstärkte schnellhärtende Prepregs und kurzfaserverstärkte Formmassen im unreagierten Zustand im Duroplastspritzguss. Der realisierte Herstellungsprozess mit nur einem Werkzeug und einer Maschine ist hinsichtlich Ressourceneffizienz und Wirtschaftlichkeit zukunftsweisend. Die Einsparung an Energie und Fertigungszeit beträgt über 50 %. Zudem wird durch die Infiltration der Füllstoffe in die Zwischenräume der Endlosfasern beim Anspritzen und der gemeinsamen Vernetzungsreaktion die Verbundfestigkeit zwischen beiden Werkstoffen gegenüber vergleichbaren Hybridbauteilen deutlich gesteigert. Neben der Erforschung der Grundlagen zu Prozessführung, Grenzflächenentstehung und Umformung, umfasst das Projekt Duro-IMF auch die Entwicklung von Handling, Werkzeug und die simulative Abbildung.